In the last 20 years, truck diagnostics have evolved in many ways, and for manufacturers, the evolution continues. Today's truck, tractor, and trailer systems increasingly sport highly advanced telematics and remote diagnostic capabilities. The manufacturers' senior executives discussed their products' latest features and benefits, along with future growth plans. Their comments have been edited for clarity.
Panel of Experts
- Patrick Brown, Mack senior strategy and sustainability manager
- Patrick Wallace, Peterbilt marketing manager for zero-emission and connected truck
- Magnus Gustafson, Volvo Trucks North America VP of connected services
- Scott Blair, Lynx Fleet Telematics senior digital program manager, Carrier Transicold Truck/Trailer/Rail Americas
FleetOwner: How has remote diagnostics evolved, and what are your system's latest features and capabilities?
Patrick Brown, Mack: Diagnostics were once primarily done after a problem occurred and the truck was at a shop. However, there was very little information about how and when an issue occurred, what the truck was doing, and what else was happening at the time of the failure. With the advent of monitoring services like GuardDog Connect, diagnostics began to incorporate real-time information, allowing a better understanding of the root cause of a failure.
Today, there is much more processing capability for fault codes, which allows for more accurate diagnosis. Remote monitoring can detect issues before they become serious, and manufacturers can notify customers of the severity of the problem and send detailed repair instructions to remedy the situation.
Patrick Wallace, Peterbilt: Diagnostics have become more convenient and accessible for fleets and dealers to get actionable information. With Peterbilt's SmartLINQ line of connected services, we offer remote diagnostics for engines and aftertreatment systems that feature fault codes and historical sensor data. That information is helpful to fleet managers and technicians as it speeds up intake at repair facilities and increases uptime.
Magnus Gustafson, Volvo: Volvo Remote Diagnostics has evolved with systems updated with analytics capabilities, AI, machine learning, and predictive models. This provides more accurate alerts and notifications. With Volvo Connect, we have added visualization layers so customers know what is happening with any vehicle. In addition, with Volvo Remote Programming, we can send software updates directly to the vehicle, often when the driver is resting, to improve performance and help prevent unplanned downtime.
Scott Blair, Carrier Transicold: Remote diagnostics are evolving to meet the needs of more specific commercial vehicle applications, and the cold chain is a good example. Shippers of food, pharmaceuticals, and other high-value, temperature-controlled cargo have high standards for compliance, accountability, and uptime. Integrating telematics with a transportation refrigeration unit delivers the monitoring, two-way control, and support these fleets and their customers require.
For example, real-time alerts and exception-based reporting take on added significance for reefer fleets. Operations and maintenance managers want to be notified automatically when something happens that can affect conditions inside the vehicle, such as deviation from temperature setpoints or a low battery or fuel level.
Lynx Fleet makes remote diagnostics data actionable. It can send a comprehensive report on the TRU engine, compressors, evaporators, temperature probes, and other parts and identify trends in equipment performance data.
See also: Bestpass integrates toll data with Geotab telematics
FO: How do the latest innovations in telematics benefit fleets?
Gustafson: Generally, the latest innovations provide insight into the performance of a vehicle or a fleet. By understanding how trucks operate, fleets can compare specs and make data-driven decisions. Having that insight and visibility also helps control operations, remotely set and program-specific operating parameters, and provide fleet managers with a means to control costs and adjust to external factors such as fuel prices.
Blair: The latest innovations focus on remote monitoring and programming for TRU diagnostics and service. Fleets can download information recorded by controllers, including temperatures, unit run-time, and other diagnostic information, and perform over-the-air software updates.
Wireless data transfer can also reduce the need for technicians to walk the yard to manage equipment. Efficiencies are gained through remote unit activation and setpoint management, automated pre-trip inspections, hands-free trailer precooling, remote software updates, and wireless data downloads. The result can be a substantial labor savings.
Wallace: The latest innovations are really integrations. Fleets want to avoid installing aftermarket hardware and utilize software not optimized for the truck. They want to have their applications interact with the truck systems seamlessly while giving a consistent user experience to the driver and fleet manager across platforms. Having the trucks always connected also enables over-the-air updates.
Brown: Fleets gain many benefits from telematics, including visibility and control. With the recent launch of Mack Connect, our customers have much better visibility of performance, including where trucks are and detailed information about fuel use and safety. The portal also shows any GuardDog Connect diagnostics cases with detailed information about the issue detected and repair instructions.
FO: What role do remote diagnostics play in the ongoing development of predictive and prescriptive maintenance practices?
Blair: Depending on the Lynx Fleet service arrangements, fleets, and dealers can monitor TRU performance collaboratively. Before a driver is even aware of a potential issue, a dispatcher can receive an alert and, with the dealer's help, determine whether the problem is critical. With the data the TRUs supply and by leveraging our expertise as the OEM, Carrier is developing analytical models to help customers better manage their assets by identifying potential issues before they occur.
Brown: The information gathered from GuardDog Connect services enables better failure recognition. We can also intervene before issues worsen and increasingly predict problems based on AI.
Gustafson: By collecting data continuously from trucks, we can analyze patterns, find correlations, and tweak programming models. Incorporating actual repair order data and/or warranty claims, we can help customers maximize the life of components and dynamically optimize their maintenance schedules. This helps save on maintenance costs and avoid unnecessary downtime.
Wallace: Remote diagnostics are an essential stepping stone to predictive technologies. You need the data to see what issues are arising and what patterns emerge that contribute to those issues. With the proper codes and accompanying sensor data, you have the information to build predictive data models.
FO: What future diagnostic developments do you envision?
Brown: Mack will continue to expand the capabilities to detect and accurately diagnose as many issues as possible. Increasing the use of AI will be a key enabler. Hundreds of thousands of data processed through an AI engine can identify and quantify issues on a macro and individual truck levels and help fleets move toward identifying problems before they become failures.
Wallace: We envision more systems being brought into the remote diagnostics umbrella besides engine and aftertreatment. In addition, Peterbilt wants to further enable remote interactions with the truck with new functionalities.
Blair: Analytics and dashboards will become even more critical as fleets learn to analyze the data they're collecting. The information can also be shared with most major transportation management systems for one-way monitoring and two-way control. When fleets have a mix of refrigeration units and telematics, integrating inbound unit data through a TMS provides a complete overview of all refrigerated assets, regardless of make.
Gustafson: We believe AI will play a significant role in the future. Sharing and providing access to key truck attributes is something we are exploring to provide actionable insights that will help ensure customers can maximize the performance and value of their trucks.
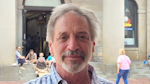
Seth Skydel
Seth Skydel, a veteran industry editor, has more than four decades of experience in fleet management, trucking, and transportation and logistics publications. Today, in editorial and marketing roles, he writes about fleet, service, and transportation management, vehicle and information technology, and industry trends and issues.