As tank container usage booms, Quality Carriers debuts intermodal service
The use of ISO tank containers in transportation, particularly overseas in Europe and Asia, has grown exponentially over the last two decades, going from approximately 200,000 containers through the mid-2000s to nearly 800,000 this year, according to the International Tank Container Organization’s (ITCO) 2022 Global Tank Container Fleet Survey.
The Houston-based Intermodal Tank Container Association (ITCA) anticipates 1 million tank containers in global operations by 2025—with U.S.-based shippers and carriers finally increasing domestic adoption to address supply chain, capacity, and sustainability issues.
“The problem here is our shippers have become spoiled,” said Steve Benet, ITCA committee member and deputy director for bulk transport equipment at VSP Technologies. “They want everything right now and that’s driven freight over the road. But as economics fix that issue, we’re going to have to start looking more like Europe, where the intermodal equipment is barged, and you have a truck-rail-truck concept.”The North American transition is already occurring—and Quality Carriers is in a leading position.
The CSX Transportation-owned bulk liquid carrier launched an intermodal, truck-rail-truck service in September after receiving the first production units of a patent-pending, 20-foot ISO tank built by South African manufacturer Welfit Oddy, which Quality Carriers President Randy Strutz says addresses issues restricting domestic acceptance. They were up to 51 units recently—and planned to have 150 in service by the end of the year.
Exponential growth
Benet and Ron Beeson, global transportation and logistics manager for The Lubrizol Corporation, presented ITCA’s take on current and future opportunities and obstacles in the tank container industry—and potential impacts on tank truckers—during a crossover event at National Tank Truck Carriers’ 2022 Tank Truck Week in Houston.
They said efficiency and flexibility are driving the proliferation of ISO tanks, which can hold most bulk materials and move via any transportation mode, from over-the-road trucks to rail, barge, and steamship. That’s why “these ISO containers will become more prevalent than any other mode of transportation,” Benet asserted.
See also: How in-cab technology is changing tank trucks
Tank container manufacturers produced 50,000 units last year. They were only making 15,000 a year in the mid-2000s, according to ITCO’s survey. “In 2022, 2023, and 2024, you’re going to see in the neighborhood of 60,000 to 80,000 tanks manufactured globally each year,” Benet said. “The thing driving this is simply economics.” He also pointed out one road tanker costs approximately $100,000, which can buy “five or six” ISO tanks that also can be utilized as drop-in storage. Beeson said one Lubrizol facility had close to 100 tanks of loaded storage the company unloaded as needed.
“They don’t have road tankers like we know them in other parts of the world because of the way they utilize the tank container,” Benet said.
None of the top tank manufacturers are in the U.S. Strutz said Quality Carriers went to one U.S. manufacturer who previously built ISO tanks, but they declined to participate after reviewing their design, so he turned to Welfit Oddy. Only a handful of the top tank container leasing companies in the world, like CS Leasing, are U.S.-owned. The top three are EXSIF Worldwide, a wholly owned subsidiary of Berkshire Hathaway, with 71,350 units, Eurotainer (51,500), and Seaco Global (42,000).
But the leading ISO tank operators—like Stolt Tank Containers, with 43,000 tanks, and Hoyer Group (35,500)—are increasing their U.S. presence. Garth Belue, president of Groninger Cleaning Systems in the U.S., said operators are building more tank cleaning capacity in Houston than anywhere else in the country, and Stolt currently is expanding its Houston facility to go from cleaning up to 80 containers per day to 250 a day.
“It’s going to grow here in the United States,” said Belue, citing imports, exports, and domestic movements as drivers.
Domestic design
Quality Carriers already has 300 40-ft. containers, with about 70 in intermodal service, and Strutz expects to grow their 20-ft. ISO tank fleet to 1,000 units by the end of 2024.The carrier took delivery of the first prototype unit in February. The tanks, for which Quality Carriers is pursuing a patent, have two key modified features Strutz said shippers and consignees already appreciate: U.S.-compatible fittings and improved vapor recovery. And they’re loading them on newly designed sliding drop-deck chassis.
Quality Carriers’ U.S. supplier ships the valves and fittings to South Africa, where Welfit Oddy incorporates them into the tanks, which are imported through Charleston, South Carolina at a rate of approximately 10 per week. “We made sure all the valves and fittings were standard U.S. fittings, as opposed to British or metric fittings,” Strutz explained. “And while that may sound minor, it’s a big deal for drivers, especially unloading. We have all the same hoses, same equipment, same familiarity with the valves.”
Vapor recovery, which keeps the tank from collapsing during unloading, is at ground level. “We’re basically capturing the fumes, making them a part of the delivery process, and keeping them within the tank,” Strutz said. “Vapor recovery isn’t standard on an ISO tank, so we designed it in. And some people thought it wasn't possible because there wasn’t enough room, but we figured it out.”
Chassis are sourced from one international and two domestic suppliers, Strutz said. They’re extended to 40 ft. for transport to meet weight and axle spacing requirements, then retracted for unloading so the trailer’s rear is flush with the tank. “You can imagine trying to hook up a heavy, stainless-steel hose to something 10 ft. away and trying to navigate the axles and frame and climb over them to get to the tank valves,” Strutz said. “It’s not safe, so we didn’t like that, and many receivers of chemicals say you can’t bring them in because they don’t want their people climbing around with big hoses and trying to hook them up.
“So we designed a new slider chassis that solves the problem.”
Tanks arriving on a direct route from South Africa to Savannah are loaded onto the new trailers, delivered to Quality Carriers’ North Charleston maintenance shop for inspection, placarding, and plating, and then distributed to customers. Two primary rail routes are from St. Louis and Jacksonville to New Jersey. Containers are shipped two per well car—sometimes with a 40-ft. tank filled with dry bulk on top.
“Customers love the service,” Strutz said. “It’s reliable and very truck-like. So if truck transit is two days, we’re able to do it in three. They like that. It’s predictable and efficient. And they also like that they’re seeing some cost savings.”
Future efficiency
Further ISO tank benefits include durability and structural integrity—allowing the tanks to be stacked up to nine high for space savings—sustainability (the tanks are 95% recyclable, ITCA said), and “door-to-door” convenience. That’s why Benet insists they’ll be utilized here for more than imports and exports as container operators expand their networks.
“You’re going to see these ISO tank carriers operate with a much more efficient ability than if they were dealing with a third party (like a trucking company), and that’s going to directly affect shippers, to where they can have the same product delivered wherever they need it for less money,” Benet said.
“If you invest in an ISO tank today, you can guarantee yourself you’re going to be using that tank 20 or 30 years down the road,” he said. ISO tank adoption also is way to address the growing driver shortage, and delays in truck and trailer deliveries, they concluded. “If we can do truck-rail-truck efficiently, it’s a legitimate solution,” Beeson said.
However, significant hurdles remain, including U.S. highway weight limits, consignee acceptance, loading rack compatibility, and developing U.N. requirements for tank baffles to prevent product surge during shipping that also complicate cleaning. Strutz estimated their 20-ft. tanks weigh 8,000 lb. and the slider chassis weigh 10,000 lb., so with 40,000 lb. of product, they’re already approaching 60,000 lb. without the tractor. Tractor-trailers here are limited to 80,000 lb. gross vehicle weight, unlike in Europe, where limits are higher.
“Everything gravitates toward efficiency, and the ISO container industry has benefited from that,” Beeson said. “It faces some of the same challenges the over-the-road industry does, but the growth is obvious.” That’s why the bulk industry, including carriers, shippers, and equipment lessors, needs to work together to develop a long-term solution, Beeson and Benet maintained.
But Strutz is convinced tank trailers—and those who haul them—will always have a place in the U.S. bulk liquid supply chain.
“You have to move a certain amount of distance for the economics to make sense,” said Strutz, comparing intermodal vs. OTR service to flying vs. driving. “It doesn’t make sense to fly from Houston to Beaumont, for instance, when it’s still cheaper to drive. You have to go a certain distance, probably 400 to 500 miles, so the math works.”
This article originally appeared on Bulk Transporter, one of FleetOwner's sister sites within Endeavor's Commercial Vehicle Group.
About the Author
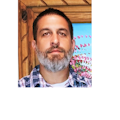
Jason McDaniel
Jason McDaniel, based in the Houston TX area, has nearly 20 years of experience as a journalist. He spent 15 writing and editing for daily newspapers, including the Houston Chronicle, and began covering the commercial vehicle industry in 2018. He was named editor of Bulk Transporter and Refrigerated Transporter magazines in July 2020.