Improving uptime: How diagnostics and telematics create comprehensive maintenance plans
Telematics systems and data are crucial for executing effective maintenance plans, noted Alex Clementi, pre-sales engineer at Decisiv. "Meter data, especially, is essential for keeping track and making sure you're current on PM schedules," he emphasized. "Any maintenance schedule that's based on mileage or engine hours needs constantly updated meter data to ensure you're within the interval you've set for your maintenance parameters."
"Diagnostic data in the form of trouble codes is valuable as well," he continued. "Codes that come up on a regular basis point to areas where you may need to adjust maintenance plans. They also let you determine if there are specific components that need more attention or maybe a shorter maintenance interval."
Diagnostic data can provide historical data points that identify trends over time with specific model years and makes of equipment, Clementi noted. With that information, he added, you can make better decisions and adjustments to maintenance plans.
Onboard telematics devices have enabled fleets to pair their diagnostic tools with remote diagnostic applications for around-the-clock monitoring of their entire fleet, according to Jason Hedman, product manager at Noregon. "Remote diagnostics offer the obvious benefits of monitoring vehicles while on the road, but additional uses exist, such as easing the pre-trip inspection process.
"Rather than walk around the yard and connect a diagnostic tool to each tractor to ensure it is road ready, fleets can use applications like TripVision to create geofences around their facilities and view the health, safety, and performance status of each asset," Hedman explained. "Additionally, fleets can use the same geofences and create alerts if a vehicle leaves the facility with a health or safety issue."
"Historical data is also a key piece of the puzzle in diagnosing recurring issues," Hedman added. "Our JPRO diagnostic tool includes a Fault History feature that allows technicians to view the faults from previous JPRO connections on that asset."
See also: Akin: Prevent fuel theft and fraud with telematics
For Dave Shock, Nexiq Technologies product manager, fleet owners and repair operations can use diagnostics, telematics, and historical data to monitor a vehicle's performance and identify potential problems that can be addressed during routine maintenance.
"Using a diagnostic tool, a technician identifies the issues, which are recorded in the repair order, along with information such as engine hours, fuel consumption, and miles driven," Shock explained further. "A fleet manager can then analyze this information against historical and telematics data to identify a trend or pattern."
"Through this process, a repair facility can predict future vehicle breakdowns and address potential problems during routine scheduled maintenance before they occur," he continued. "That not only improves uptime but also helps reduce costs."
Diagnostic and telematics devices play crucial roles in accumulating information, Shock noted. For diagnostics, a wide range of solutions are available, including eTechnician commercial vehicle PC-based diagnostics from Nexiq, which can diagnose engines, transmissions, brakes, bodies, and chassis on commercial vehicles.
"Fleets should take advantage of any technology that helps them improve safety and uptime, whether it's through improved maintenance processes or quicker detection of serious faults," Hedman said. "Fortunately, thanks to the proliferation of telematics, many fleets already have the technology on their vehicles to begin monitoring them in real-time."
For fleets and service providers, automating the process of receiving diagnostic data is a game changer, Alex Clementi noted. "Across different telematics providers and systems and fleet and asset management solutions, including the Decisiv SRM platform, you now have information sent to you instead of having to access that data or keep track of it on your own," he said. "Those tools and technology are the key to reducing and preventing unplanned, unscheduled downtime."
About the Author
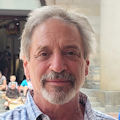
Seth Skydel
Seth Skydel, a veteran industry editor, has more than four decades of experience in fleet management, trucking, and transportation and logistics publications. Today, in editorial and marketing roles, he writes about fleet, service, and transportation management, vehicle and information technology, and industry trends and issues.