Each year U.S. fleets use about 3 billion gallons of diesel fuel idling. That equates to 8% of total fuel burned. Sadly as much as 2 billion gallons were unnecessarily used because the industry failed to take advantage of existing idle-reduction technology.
Unfortunately many fleets aren’t aware of all the idle-reduction technology options out there and the plethora of options can be very confusing. We, Trucking Efficiency, an effort to double the efficiency of NA goods movement, looked at the idle-reduction technology landscape to see which technologies could help fleets meet their goals.
Right off the bat we discovered a few really basic things that help. Extra sleeper and cab insulation make any idle-reduction solution more efficient. And something as simple as painting the cab a light color versus dark reduces the thermal load. Did you know it requires 20.3% less energy to cool a white cab than it does a black cab? Something to think about.
But it’s using one technology as an anchor and combining it with complementary technologies that can work best. Consider these choices when trying to reduce idling:
- Diesel APUs combined with additional insulation, an inverter and a fuel-operated air heater uses the least amount of heat to meet idle-reduction and driver comfort goals.
- With battery HVAC systems fleets pairing extra insulation, a fuel-operated air heater, an automatic engine start/stop system and/or off-board AC power or truck stop electrification will see good results.
- Automatic engine start/stop systems when paired with Clean Idle engines are a good choice for maintaining sleeper temperatures and battery charge.
- Truck stop electrification is not widely enough available to be a complete solution for a fleet’s idling needs. But when paired with a fuel-operated air heater and an inverter/battery charger it’s a good option for trucks running dedicated routes.
- For fleets looking to make a minimal investment in idle-reduction technology, using fuel-operated air heaters and engine parameters to regulate allowed idling conditions coupled with driver training and incentives is an inexpensive way to keep drivers warm.
Idling costs fleets money and even without regulations limiting it, investing in technologies that lower idle time, reduce fuel costs and wear and tear on the main engine. Picking the best combination of solutions is the key.
Check out this short video for more information on the study findings:
For a complete copy of the report go to www.nacfe.org
About the Author
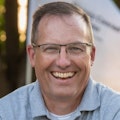
Michael Roeth
Executive Director
Michael Roeth is the executive director of the North American Council for Freight Efficiency. He serves on the second National Academy of Sciences Committee on Technologies and Approaches for Reducing the Fuel Consumption of Medium and Heavy-Duty Vehicles and has held various positions with Navistar and Behr/Cummins.